La NASA ha desarrollado una nueva superaleación llamada GRX-810, que es el doble de fuerte y más de 1000 veces más duradera que las superaleaciones impresas en 3D de última generación. La aleación de alta temperatura podría usarse para construir piezas más resistentes y duraderas para aviones y naves espaciales.
NASA has developed a new superalloy called GRX-810, which is twice as strong and more than 1,000 times more durable than the state-of-the-art 3D printed superalloys. The high-temperature alloy could be used to build stronger and more durable parts for airplanes and spacecraft.
NASA has demonstrated a breakthrough in 3D printable high-temperature materials that could lead to stronger, more durable parts for airplanes and spacecraft.
A team of innovators from NASA and The Ohio State University detailed the characteristics of the new alloy, GRX-810, in a peer-reviewed paper published in the journal Nature.
“This superalloy has the potential to dramatically improve the strength and toughness of components and parts used in aviation and space exploration,” said Dr. Tim Smith of NASA’s Glenn Research Center in Cleveland, lead author of the Nature paper. Smith and his Glenn colleague Christopher Kantzos invented GRX-810.
Smith and his team employed time-saving computer modeling, as well as a laser 3D printing process that fused metals together, layer-by-layer, to create the new alloy. They used this process to produce the NASA logo pictured above.
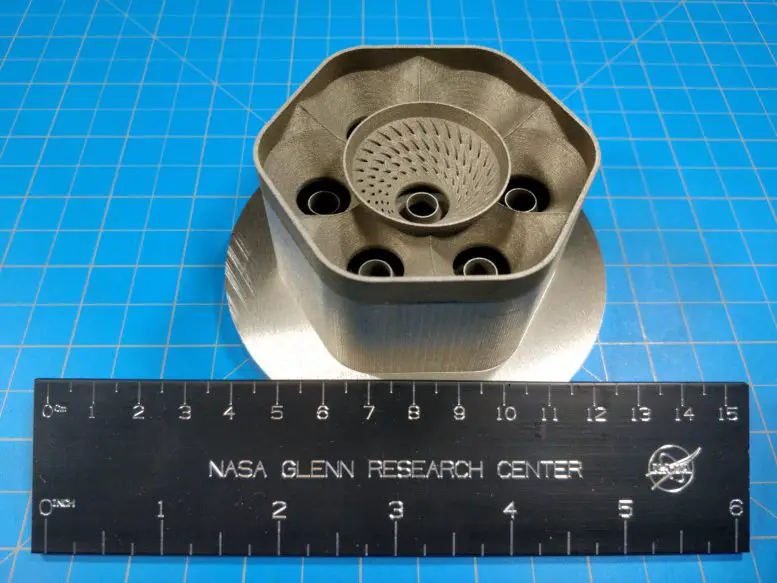
GRX-810 is an oxide dispersion strengthened alloy. In other words, tiny particles containing oxygen atoms spread throughout the alloy enhance its strength. Such alloys are excellent candidates to build aerospace parts for high-temperature applications, like those inside aircraft and rocket engines, because they can withstand harsher conditions before reaching their breaking points.
Current state-of-the-art 3D printed superalloys can withstand temperatures up to 2,000 degrees Fahrenheit. Compared to those, GRX-810 is twice as strong, over 1,000 times more durable, and twice as resistant to oxidation.
“This new alloy is a major achievement,” said Dale Hopkins, deputy project manager of NASA’s Transformational Tools and Technologies project. “In the very near future, it may well be one of the most successful technology patents NASA Glenn has ever produced.”
A team of contributors from Glenn, NASA’s Ames Research Center in California’s Silicon Valley, NASA’s Marshall Space Flight Center in Huntsville, Alabama, and The Ohio State University co-authored the Nature paper.
GRX-810 was developed under NASA’s Transformational Tools and Technologies project, with support from the agency’s Game Changing Development Program.
Reference: “A 3D printable alloy designed for extreme environments” by Timothy M. Smith, Christopher A. Kantzos, Nikolai A. Zarkevich, Bryan J. Harder, Milan Heczko, Paul R. Gradl, Aaron C. Thompson, Michael J. Mills, Timothy P. Gabb and John W. Lawson, 19 April 2023, Nature.
DOI: 10.1038/s41586-023-05893-0
Fuente: https://scitechdaily.com