El proyecto LOXODON -1 iniciado en 2019 en Puerto Rico, servirá como prueba de I&D conceptual para el desarrollo de futuros motores de cohetes y servirá a los estudiantes para enriquecer la etapa de formación de sus carreras profesionales. Entre sus objetivos esta: El diseño de un motor de 200 Lb / fza de empuje; Desarrollar un banco de pruebas para verificar el comportamiento del motor frente a las exigencias termomecánicas, registrando y recopilando los parámetros del ensayo; preparar la próxima generación de científicos espaciales portorriqueños, como primer paso para el desarrollo de la industria espacial de ese país. El equipo está trabajando además para competir en la copa “America Spacecraft” en un futuro próximo.
Started in the spring of 2019, this project will serve as a proof-of-concept for future engines and prepare the students for their professional careers. In addition, the team is working to compete in the Spaceport America Cup in the near future. Some of it’s objectives are to:
-
Produce 200 lbf (pounds of force) thrust at sea level
-
Develop a test stand capable of withstanding the engine’s forces and collecting data from the test
-
Prepare the next generation of Puerto Rican rocket scientist and develop the space industry in PR.
The team is divided into 5 divisions: Propellant Systems, Engine Development, Test Stand, Safety & Mission Assurance, and Business. More information on these can be found below.
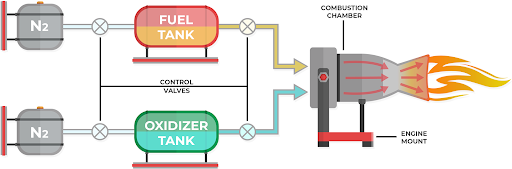
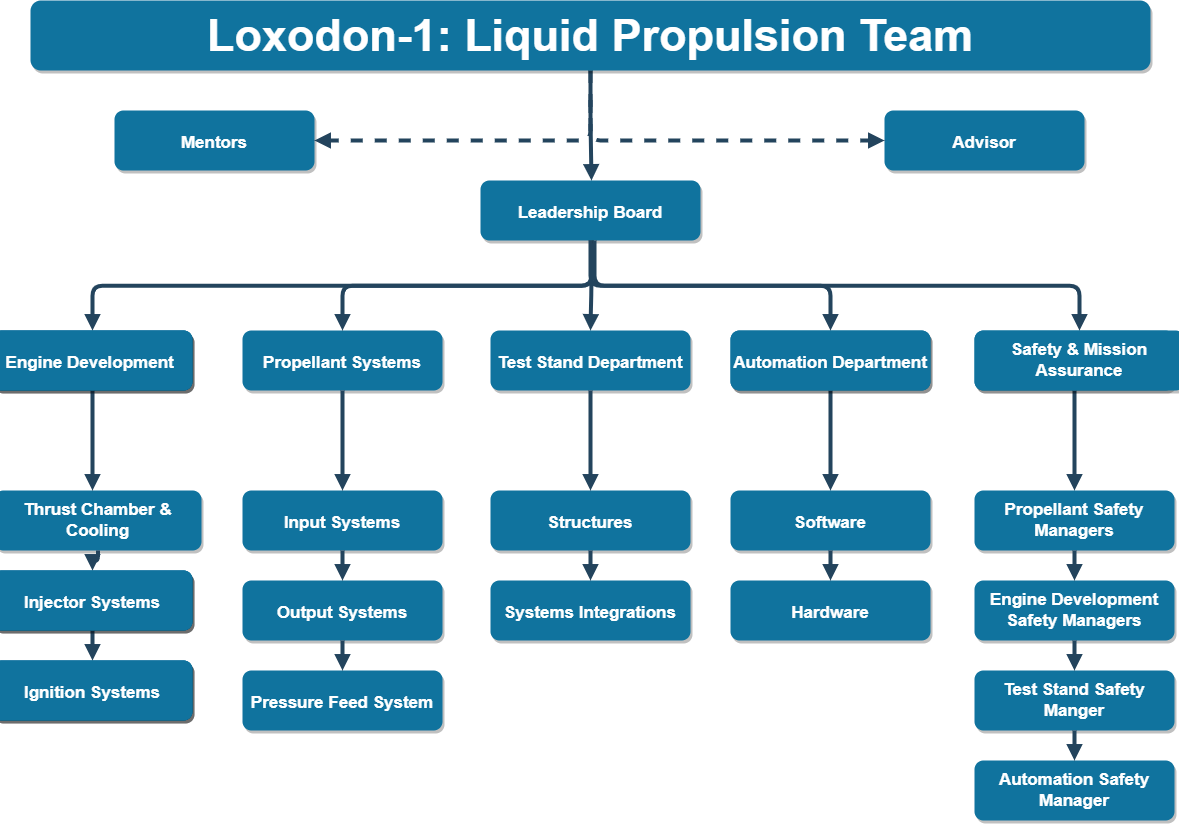
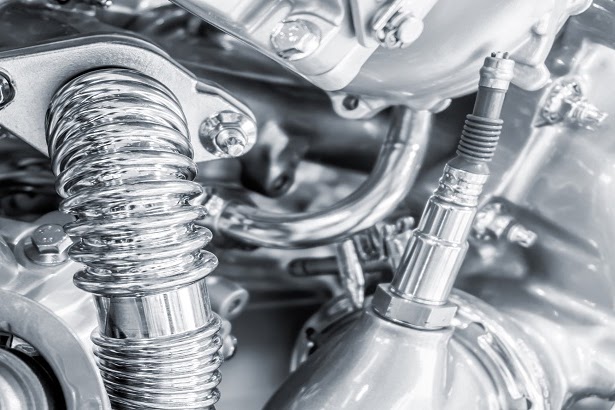
The engine development division works on the design and analysis of the injector plates, manifolds, thrust chamber, cooling and ignition system. Most of their work has been focused on researching the optimum design calculations for the engine and validating the data found. With the help of mentors, various refined CADs (Computer Aided Design) have been produced for the different engine components. These CADs have also undergone thermal, pressure, and vibration simulations to validate the designs. The team is looking forward to completing the simulations and begin prototyping.
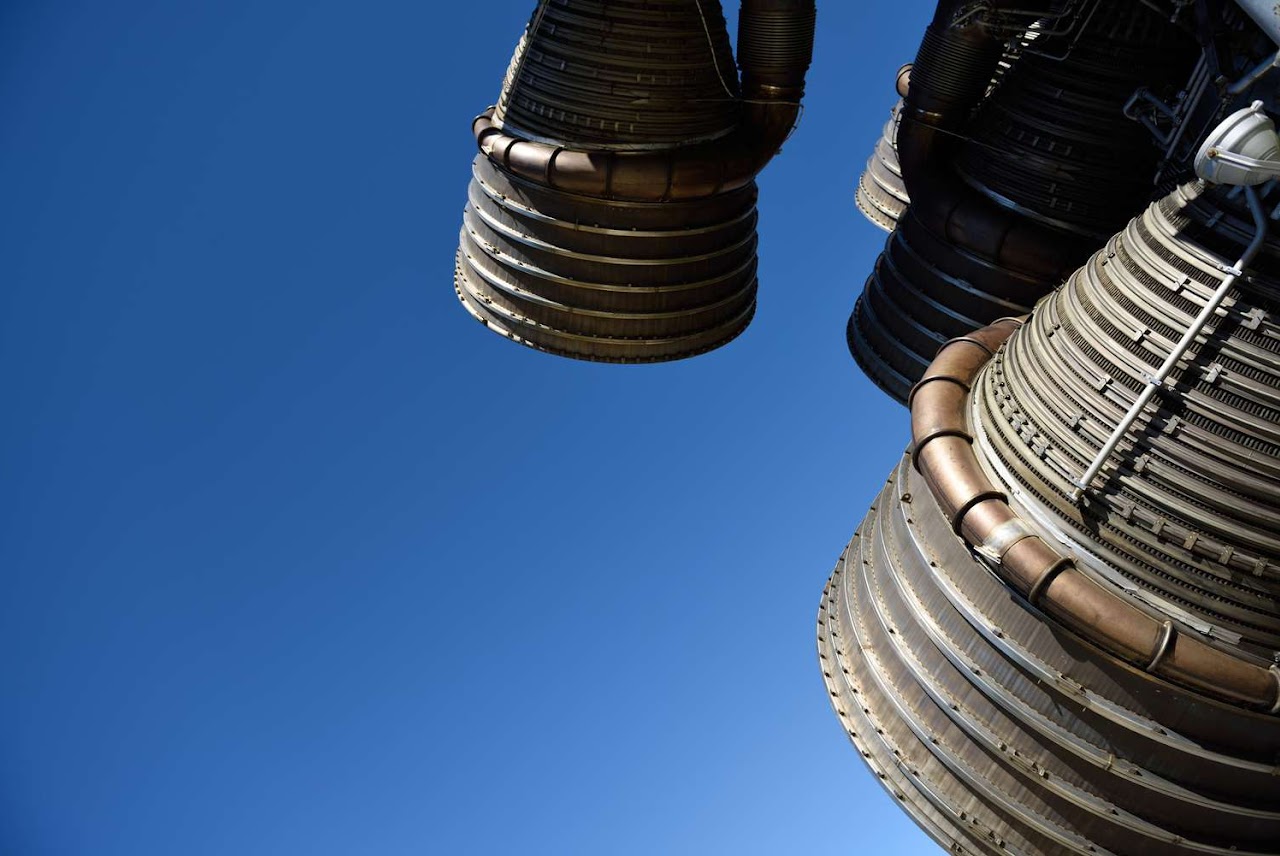
The test stand division is divided into two sections: Structure and Automation. The Structure division is responsible for creating the platform that will hold the engine, tanks, and piping system. They focus on creating a sturdy stand that will be able to uphold the forces and vibrations caused by the engine during a hot fire test, while also measuring data for future analysis. They are also responsible for the safety barracks where all the members will be protected in case objects are ejected or a RUD (Rapid Unscheduled Dissassembly) occurs. As of now, they have begun the test stand prototyping.
Automation, on the other hand, works with the testing logistics and the technologies needed for data acquisition. Their work is mostly focused on creating programs and setting up instrumentation to properly measure and analyze all the data collected, while still surviving the extreme heat and forces present during the hot fire test.
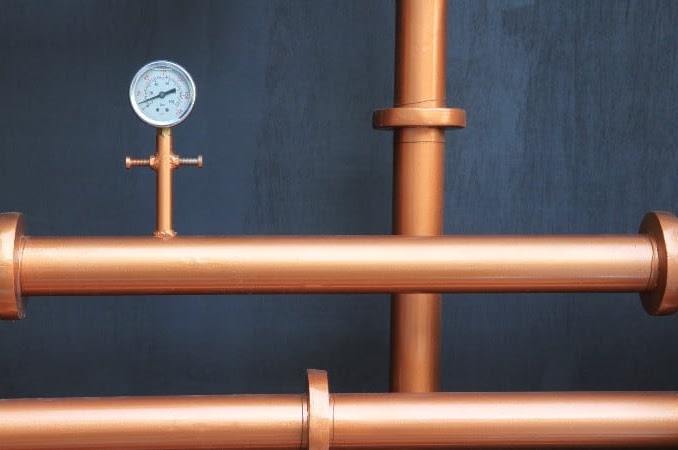
The Safety & Mission Assurance division works closely with all of the other division to identify and asses possible risks and produce mitigation plans. They create 5×5 Risk Matrices (Likelihood vs Consequence) to categorize every possible hazard, affecting both personnel and the mission assets. A Fault Tree Analysis is also utilized to evaluate causes and effects for failures. Their most important task is to ensure the safety of our members, thus many mitigation plans are produced and the testing logistics are carefully analyzed.
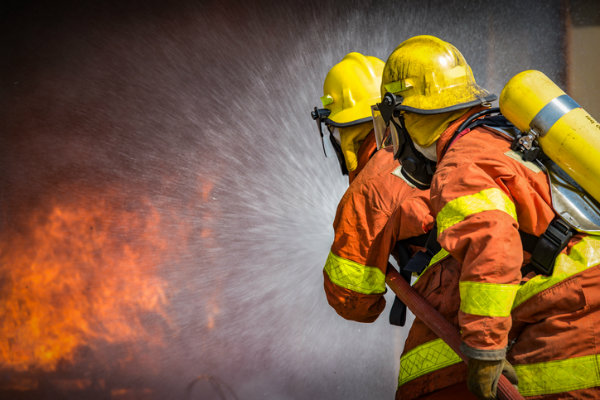
Help others get up to speed with the project concept and goals with 2-3 summarizing sentences and clearly state the status of the division – on track, at-risk, or behind. Provide context for what was shared in previous reports and more detail on what to expect in the next 30 days. Bring transparency to shifts in the division’s strategy, roadblocks, milestones, and upcoming action items.

Fuente: https://sites.google.com